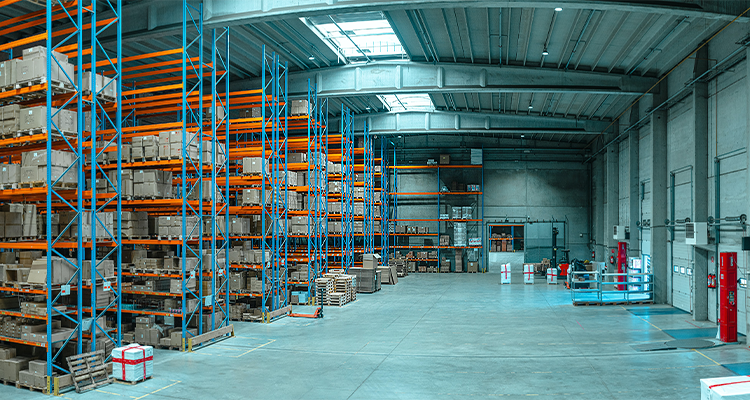
Electric vehicle revolution triggers transformations in automotive supply chains. By Mike Hitmar
The soaring popularity of Electric Vehicles (EVs) has changed the face of the automotive industry forever. Recent EV sales figures in Europe indicated a 40 percent increase over the last five months. However, manufacturers face significant challenges as they strive to produce vehicles rapidly, with industry leaders quickly responding to the spike in demand. Panasonic recently recognized the need for four more EV battery plants if supply is to meet demand, whilst Jaguar Land Rover has outlined plans to create an exclusively electric production plant by 2025.
As automotive innovation accelerates, companies are working to ensure their supply chains keep pace. Automotive supply chains are incredibly complex, and EVs only add to their intricacy. In the past, isolated decision-making, lack of connectivity, and poor data hindered supply networks. With geopolitical conflicts continuing to squeeze supply, many manufacturers are adopting technology that facilitates proactivity. The automotive industry is entering new territory, and companies should consider adapting their supply networks to align with it.
Rerouting: ensure intricacy doesn’t lead to disarray
Unprecedented demand shifts extend from manufacturing and charging stations to software and firmware updates. Chaotic swings in automotive supply and demand can risk customer loyalty. Customers will head elsewhere if vehicles aren’t readily available, so consistent supply is non-negotiable.
Poor visibility of inventory across suppliers means poor visibility of supply risk. A single issue among thousands of suppliers over multiple tiers can make even the most efficient production lines grind to a halt. Due to the complexity of new vehicles and the myriad required parts, manufacturers and suppliers often turn to overstocking as a solution. This can exacerbate shortages and tie up capital that may be put to better use elsewhere.
With a proliferation of configuration options, a shift from make-to-stock to make-to-order, and the surge in new suppliers for novel technologies, the complexity only grows. Disruptions now span demand and supply, requiring manufacturers to monitor multiple stakeholders, from systems, components, and materials, to dealers, customers, and recyclers, and consider building new supplier relationships when necessary. Manufacturers also require visibility to ensure this further complexity doesn’t equate to delays.
No easy wins when it comes to shortages
Shortages of semiconductors and metals for EV batteries continue to plague the automotive industry. In 2021 alone, the industry lost $210 billion in revenue due to chip shortages slowing or stopping vehicle production altogether. And when the industry only uses five-to-ten percent of semiconductors, with most going to consumer electronics, automotive manufacturers often find themselves at the back of the queue. Some even have to choose which features to include on vehicles to try and keep up with demand, leading to costly retrofits to give customers the functionality they want. With no foreseeable end to the shortages, leaders seek creative ways to bolster their supply chains and meet demand.
Shortages aren’t fully solved by finding new suppliers and creating an extended supply chain. More suppliers equal more risk of weather disruptions, port bottlenecks, and labor shortages, and every supply chain link should be closely monitored to handle issues proactively. Some have turned to nearshoring to produce parts locally and alleviate these risks. However, a lack of raw materials can cause manufacturers to continue to source components from further afield – and the complexity continues. Ideally, short-term fixes will be combined with longer-term planning, allowing automotive leaders to balance suppliers and strengthen stock effectively.
Fueling up for the road ahead
Connecting the dots between a wealth of suppliers and stakeholders may seem challenging. But it’s a smart move for manufacturers looking to create collaborative, ‘future-proofed’ supply chains. Crucially, a connected supply chain transforms the service the end-user receives. Data-driven decisions reduce lead times and help leaders manage and monitor stock effectively.
Automotive supply previously functioned upon three elements: globalization, outsourcing, and cost-optimization. This is no longer the case as cars increase in intelligence and the case for a connected supply chain grows even stronger. Geopolitical instability and spikes in demand continue to impact the heart of supply and demand, and short-term solutions could leave leaders struggling further down the line if more intrinsic issues aren’t addressed. The automotive supply chain needs a revolution that puts visibility at the center of the matrix. With all this in place, automotive manufacturers will be set for success as the industry moves towards electric vehicles for good.
For a list of the sources used in this article, please contact the editor.
Mike Hitmar
Mike Hitmar is Director at e2open. The e2open supply chain platform is helping the world’s largest companies transform the way they make, move, and sell goods and services. Today’s supply chains are more complex, more expansive, and more reliant on external partners than ever before. With so many touch points, it is critical to have an integrated, singular platform to help you manage your extended supply chain end-to-end and respond rapidly to challenges in real time.