How to leverage three critical factors and maximize their impact on lead time planning
Everyone involved in logistics and supply chain processes understands the importance of planning lead times. However, not everyone understands that to properly plan lead times that align very closely with transit times, you must look at three different factors.
Although fine tuning the lead time process can be time consuming, effective lead time planning is a crucial part of supply chain fluidity and there are three main factors to consider:
Production time
The time it takes a factory to manufacture the quantity required to fulfil the order and constitute a shipment must be analyzed. This assumes all materials are on-hand to complete production.
Factory to distribution center transit time
This needs to be factored into lead-time planning, but distance does not present a significant challenge in today’s global supply chain. If distance was the issue, then all local consumption would be of locally made goods, so clearly this is not the case.
Collection and delivery process
Coordinating the pick-up of goods and transport to the point of departure, followed by the pick-up of goods at the point of arrival, and transport to the final distribution center represents the area with the most room for error, and therefore, has the biggest impact on lead times.
Poor administration of the pick-up and delivery processes can dramatically add to transit time, which results in either excess inventory in the warehouse or, worse, the need to build buffer stock so that there is a cushion due to poor execution. Missed deadlines can result in cargo being stuck in warehouses. Likewise, buffer stocks may be an operational reaction to anticipated problems, and penalties a commonality because of failed deliveries to retailers.
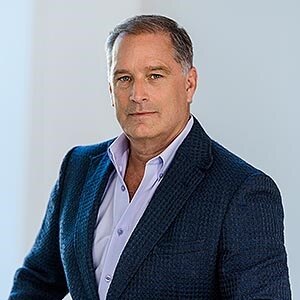
Consequences of inconsistent processes
Increased lead times are required when supply chains are inconsistent and unpredictable. So, if the administrative process is consistent, then the outcome is predictable and lead times can be reduced to no more than slightly greater than the transit time.
Administration of supply chains is a lot like project management. There are several service level tasks that go into arranging and coordinating the pick-up and delivery of freight, especially containerized freight. These tasks all involve coordination with a multitude of participants: the carrier, the terminal, the container depot, the warehouse or distribution center (appointments), and the trucker. A failure to communicate with each and every one, in proper sequence, and track the positive or negative responses from each will result in a failure in either the pick-up or delivery process.
Coordination is key
Each individual move is not unmanageable. Anyone can coordinate the load and return of one container a month: it’s a well-defined process. However, the complexity of coordination increases as cargo volumes increase.
Coordinating the pick-up or delivery of 100 containers a week is a substantially more difficult process, not because the process becomes more complex, but due to an increase in the number of individual transactions that must be made, responded to, and tracked. This makes the process less manageable and more vulnerable to errors.
The potential of automation
This is where the next generation of digitization (Digitization 2.0) comes into play. If an automated system queried the warehouse for appointments for each of those 100 containers after the booking had been made and confirmed by the carrier, then that would be 100 fewer contacts the logistics manager would need to make. Since it is machine automated, it would also be consistently executed.
Extend automation to preferred truckers for pick-up or delivery orders based on established allocations, reflecting the appointment times given by the warehouse, and again, the communication has been systematized and therefore is virtually assured of taking place.
The same concepts apply for monitoring that the trucker has responded – either positively or negatively – so that corrective actions can be taken, and alerts made.
A digital future
Overall, this would represent the mechanization automation of the key administrative processes associated with the most vulnerable part of the supply chain and the two components that have the largest impact on lead times.
The goal is to establish a uniform process and, to the extent to which consistency in this administrative process is possible, predictability of the supply chain is assured.
The overall goal is to gain a high degree of predictability in the supply chain that closely matches the transit time. This is the only way to successfully reduce lead times and consequently scale back inventory.
There is no debate in the industry today that just-in-time inventory management is the key to significant cost reduction. Just-in-time demands predictability and therefore consistency, and that can only be delivered by mechanization and automation of these administrative processes.
With more than 25 years of experience in the global logistics and supply chain industry, Bryn Heimbeck is a pioneer who champions the cloud and digitization as the most powerful new technologies in the industry. Along with Co-founder, Kevin Clark, Trade Tech was established in 1997 to leverage the internet to create a global transportation management system on a single, globally accessible, multi-tenant platform.