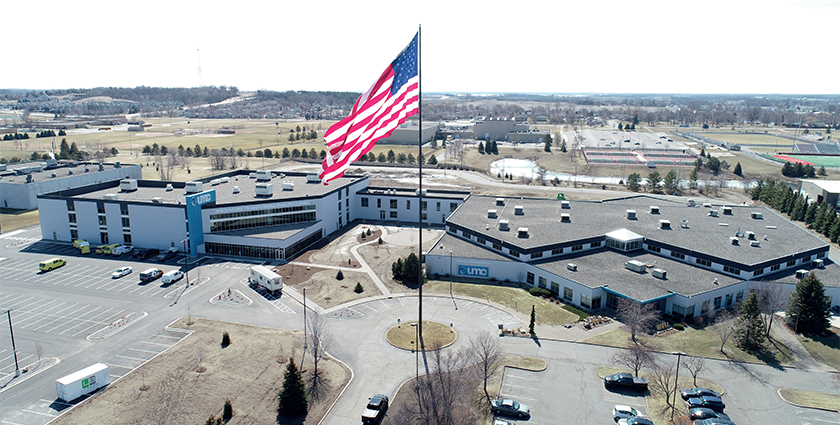
Ultra Machining Company
Precision and purpose
For 54 years, Ultra Machining Company has served as a leading precision manufacturing partner for innovators in the medical, aerospace, and defense industries. Following a mammoth expansion to its Minnesota-based factory, it intends on continuing that legacy
To show how far Ultra Machining Company (UMC) has come, it’s worth briefly returning to its humble origins. Established by Terry Tomann in 1968, the leading precision parts manufacturer initially operated out a very small facility: Terry’s garage. On a mission to create a different kind of machine shop, Terry sought to bring curiosity and technology together to go beyond simple part manufacturing and instead deliver inventive solutions that not only bolster individual projects, but also entire companies and industries.
Like-minded colleagues joined Terry, offering new opportunities for continued growth, learning, and community involvement. UMC’s relentless pursuit of continued innovation and quality improvement has led to the company’s now widely recognized status as a leading US precision manufacturer.
Terry’s son, Don Tomann, who now serves as CEO at UMC, offers an insight into the rapidly growing company: “Some of the world’s most demanding, quality-focused companies depend on us to solve their toughest precision manufacturing challenges,” he begins. “We build long-term relationships on trust, collaboration, and transparency; our partnerships are an opportunity for us to build and grow with others, elevating industries by leading with a bigger picture of what is possible. For more than half a century, we’ve focused on creating a culture of learning, innovation, and partnership, which is much needed in today’s ever-changing manufacturing world.”
As it stands, UMC has over 1400 active part numbers and over 215 employees. In 2021, it manufactured more than one million complex, precision-machined parts for clients across numerous sectors. The company specializes in difficult-to-machine materials and is recognized for its expertise, particularly with regards to projects requiring adherence to the strictest of quality standards.
UMC’s capabilities include tolerances ranging from millionths to thousandths and low micro surface finishes to exacting standards. The company offers dedicated prototyping sources, value engineering services, a fully integrated quality management system, supply chain and procurement services, and finishing and assembly processes.
More specifically, UMC provides five-, seven-, nine-, and 12-axis machining, CNC turning, Swiss machining, electrical discharge machining (EDM), and works with materials like high temperature alloys, aluminum, carbon steel, plastics, titanium, copper alloys, stainless steels, and cobalt alloys. Specialist services include anodization, laser welding, chrome plating, passivation, electropolishing, sinker EDM, grinding, heat treatment, stamping, and electrochemical etching. The list truly goes on.
All this and more takes place at UMC’s state-of-the-art facility in Monticello, Minnesota. First built in 2003, the evolving company soon began to outgrow the initial 72,000-square-foot site. Thus, earlier this year, UMC carried out a mammoth 58,000-square-foot expansion to the facility, integrating the latest manufacturing and automation technology to streamline and optimize its internal processes.
“The new UMC Innovation Center showcases best-in-class precision manufacturing capabilities and a flexible, modular footprint that allows us to experiment with automation, technology, and processes as we work with clients,” explains Don. “The facility is thermo-regulated and vibration-controlled to support the exacting environment required for precision machining; the expansion complements the existing building, creating a campus-like vibe while preserving the opportunity for us to expand as is needed. The changes reflect our wider quest to bring people and technology together to transform the future of manufacturing.
“Highlights include a wrap-around mezzanine, offering elevated views of the manufacturing floor; maximized use of glass, visually-connecting office and production areas; and manufacturing spaces that double as meeting and presentation areas,” he continues. “Large windows maximize daylight throughout the facility, and a campus-wide path and landscaped patio provide places of respite for thinking, creativity, and collaboration. Thoughtful design is at the center of what we do. By incorporating design for manufacturability (DFM), we help our customers reduce the risk of technical issues and delays arising during manufacturing, thereby increasing the probability of a successful product launch. To back that up, UMC maintains several quality assurance certifications, including AS9100D, ISO-13485, and Nadcap accreditation.”
However, never to rest on its laurels, UMC is currently exploring novel opportunities to invest in new technology and equipment to enhance its manufacturing capabilities. “As a company, we continue to procure cutting-edge technology and automation to meet the increasingly complex needs of our customers, exceeding expectations for what is possible with precision manufacturing technology,” says Don. “As we learn, we’re also preparing our facility, team, customers, and community for the future of manufacturing. The recent expansion means we can add machines and automation in a flexible, scalable way to meet both the current and forthcoming needs of our customers. To get the most out of the new site, our automation engineering team has mapped space for equipment lines, transportation, maintenance support, automation lanes, training, process development, staffing amenities, and access; they’ve also identified areas and equipment to automate ancillary services such as air and water supply, bulk fluid storage and distribution, waste metal, and waste fluid recovery systems.”
As this impressive expansion demonstrates, UMC shows no signs of slowing down – even if there are nationwide labor shortages and global supply chain disruptions. “We’ve addressed labor shortages in manufacturing for over 30 years,” says Don. “We’re involved and have invested in schools, technical colleges, apprenticeships, and other programs that introduce students to STEM and manufacturing. Our facility is also strategically placed next to the local high school, allowing us to host tours, classes, and clubs for those living in the area. People who join UMC quickly find they have access to a level of technology that they wouldn’t have anywhere else. A fundamental part of tackling labor shortages is employee retention; we’re able to retain top talent by constantly assessing and realigning employee compensation, benefits, and environments with the needs and desires of the current workforce. To that end, we recently rolled out initiatives to address employee feedback about salary, benefits, and shift schedules amid the national shortage.
“As a company, we also remain well-positioned to serve our customers during the current supply chain disruptions,” he adds. “We manage a reliable and robust supply base to maximize efficiency and customer value, maintaining optimal capacity, labor, and inventory levels. Another important part of our response to issues exacerbated by the pandemic is that we utilize closed-loop materials management, real-time tracking of production operations, and systems traceability. Our focus on continuous improvement and our use of Lean manufacturing and Six Sigma practices has allowed us to continually streamline our supply chain – despite persistent problems we are seeing crop up globally.”
Recently, UMC completed an implant project that consisted of six assembly jobs, 11 subcomponents, 352 unique assemblies, and 4,978 individual components – all within a six-month timeline. Thanks to UMC’s experience and project management capabilities, the deadline was met with ease. As it looks towards a post-pandemic future, the Minnesota-based company intends on staying at the forefront of the market it so evidently dominates.
“We’re eagerly preparing for a flexible, responsive, and data-driven future,” explains Don. “We seek out and pursue technology that maximizes peoples’ skills, imagination, and creativity. As the year goes on, we’ll keep improving our relationship with technology, data, and automation to accelerate our abilities. That way, we can continue to meet our customers’ demands and prepare ourselves, our clients, and the industries we serve for the future of manufacturing.
“Looking further ahead, we plan on adding new machines and automation to our facility to help us create better parts more efficiently for our customers,” he concludes. “We will continue to push the envelope on what is possible with precision manufacturing, leading with courage and collaboration to tackle today’s challenges while moving towards the future.”
Ultra Machining Company
www.ultramc.com
Products: Machined parts and assemblies