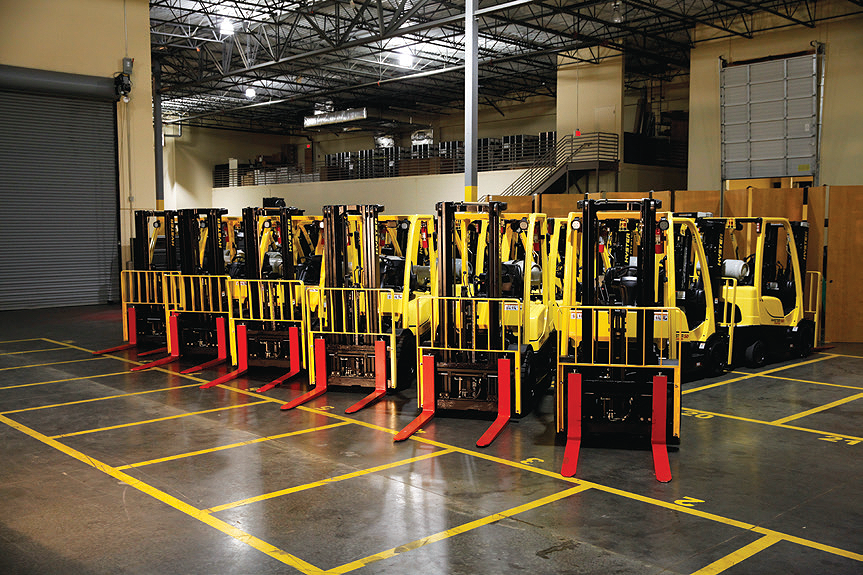
Unlock material handlingUnlock handling efficiency with data
Think back to March 2020 and the beginning of the Covid-19 pandemic. One of the most peculiar (and memorable) storylines was the great toilet paper shortage. Like bread and milk in preparation for a major weather event, toilet paper became the must-have item for consumers preparing to hunker down in quarantine.
From neighborhood bodegas to grocery stores to big-box retailers, toilet paper shelves were empty. And even when it came back in stock, retailers instituted strict rationing in an effort to prevent shoppers from hording and provide a more regular supply.
Behind the scenes, paper suppliers were scrambling to keep up and boost production – and the lift truck data supports this. We looked at a major paper product manufacturer’s lift truck fleet data and, sure enough, truck session hours rose sharply at the outset of the pandemic, indicative of the all-hands effort to address the surge. Now, what if the manufacturer knew this and acted quickly to supplement their fleet with rental trucks to cover the working time and maintain the optimal average working hours per truck?
Of course, lift truck data offers great benefit far beyond tracking the origins of a toilet paper shortage. When it comes to keeping downtime to a minimum, fleets structured efficiently and operators working at peak performance, access to the right data goes a long way. But with so much data available – related to individual operators, equipment use, individual components and more – how can fleet managers sort through the clutter?
A telemetry system sorts through mountains of data to identify the most valuable information and – here’s the important part – provides actionable insights that take the guesswork out of your work. User-friendly dashboards available online through the cloud make large data sets more manageable, even on mobile, allowing access to near real-time fleet metrics and notifications on the shop floor. Managers get notifications about things like lift truck impacts, maintenance alerts and concerns on pre-shift safety checklists for near immediate action and resolution.
It all adds up to meaningful efficiency gains in everything from labor management to fleet size and equipment procurement.
Each day, operators are required by OSHA to fill out a pre-shift safety checklist. Rather than using paper-based systems, they can use the telemetry devices mounted to equipment, complete with onboard prompts and fast alerts to key stakeholders to photograph and document any issues through the portal, informing maintenance action. Managers can customize checklist frequency to suit individual needs, and pull checklist information for a specific day, truck or operator through portal reporting tools.
To access equipment and begin the OSHA checklist, personnel must swipe a unique access card. This enables facilities to restrict equipment access only to operators with proper training and certification, and track operational data like equipment impacts and idle time by the specific employee. This increased accountability can encourage better driver behaviors, help reduce equipment damage and preserve uptime.
More recently, some manufacturers have introduced auxiliary features to provide extended functionality. One example is an onboard camera system that automatically saves footage minutes before and after an impact. Not only do supervisors get a notification if an impact registers, they get a complete picture of the circumstances around lift truck impact events. Another added feature enables lead-acid battery monitoring, gathering data on maintenance habits, watering, equalization and charging to help avoid premature wear due to mismanagement.
Optimizing lift truck size and makeup is a lot like finding the elusive ‘Goldilocks’ setting. Not too many pieces of equipment so that operations pay for lift trucks that lie dormant, but not too lean to the point any unplanned downtime grinds throughput to a halt. Utilization data helps businesses understand how they use equipment, providing the data-driven basis for decisions on fleet size and lift truck product type.
Seasonal peaks or unexpected spikes in demand may require a larger fleet than other times of year, which could lead operations to accumulate excess equipment. But using telemetry to gather and analyze utilization data can allow managers to decide on a smaller, year-round core fleet of trucks, then rely on rental agreements to handle spikes. In fact, analyzing utilization data like lift truck session hours can illuminate when spikes are happening – like those due to unexpected toilet paper demand.
While leveraging utilization data may not have avoided the impact of the pandemic on store shelves, it could have alerted managers of the need to bring in rental trucks to help handle the surge. By supplementing the core lift truck fleet, the optimal average for working hours could be maintained, helping extend equipment life and avoid unexpected service issues.
Steven LaFevers is Vice President, Emerging Technology at Hyster Company. Hyster Company offers 130 lift truck models configured for ICE and electric power, in 2,000 to 105,000-lb load capacities. Hyster also offers robotics and telematic solutions that deliver high productivity, low total cost of ownership, easy serviceability and advanced ergonomics, supported by one of the industry’s largest, experienced dealer networks.
www.hyster.com