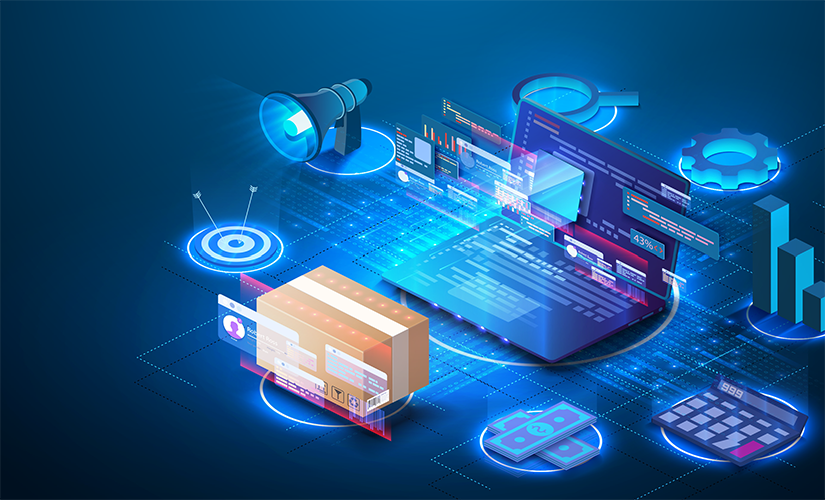
Vision picking
Logistics is the backbone of business, yet many of the processes in this industry run on outdated legacy systems that simply cannot keep up with the demand of recovery. With many businesses still contending with a huge backlog as a result of warehouse closures during the pandemic, supply chains cannot afford to experience further delays, inefficiencies and financial loss. But there is hope. Digital solutions offer the potential for increased efficiency, greater productivity, and an all-round healthier supply chain for a post-pandemic era.
One solution key to digital transformation in the supply chain is digitizing goods picking. Let’s take a closer look at the day-to-day work of an order picker and explore why vision picking is key to the future of the supply chain.
The picking process
Typically, after an order is accepted, numerous manual steps are required before goods can be distributed. This process often entails as follows:
1. The order details get logged in a system, they are then printed out as a list of goods and passed on to an employee.
2. This is followed by the picker’s (often multiple) trips to the warehouse and the picking of each item by hand, pallet truck, or forklift.
3. The employee then places the goods in the appropriate picking bin before everything can be booked out of the Enterprise Resourcing Planning (ERP) system and transferred to the packing department.
These steps can often lead to human error, long amounts of time and, therefore, large costs. One example of this is entering the order data into the ERP system. This is done by hand and can often cause typing or transmission errors. This creates inefficiencies and fragments the picking process through causing delays in the supply chain. Businesses cannot afford delays in their supply chain at any time, especially when trying to meet high demand and the current backlog. It is time, therefore, for warehouse managers to update the picking process, and ensure it is fit for the demands of recovery.
Meeting demand through digital solutions
If businesses are to meet the demands of a post-pandemic era, and set themselves up for recovery, supply chains must be fast, resilient, and accurate. Technology such as Vision Picking play a keys role in supporting employees reach their potential by bridging the gap between manual operations and warehouse automation. Pickers can be equipped with wearable technology to speed up processes and connect them to existing IT systems.
For example, after an order is sent, the order to number including the list of goods is automatically displayed on to the smart glasses via AR and displayed in the employee’s field of vision. This is similar to a head-up display in a car, where driving data, such as speed, is projected on the windshield.
The most common information in logistics provided by a vision picking system includes:
- Item (name, ID, picture, and quantity) of the good to be picked
- Storage location
- Location of destination
- Next order/storage location of the next order
- Colored markers or graphical elements to visualize status information or errors
- Audio information as confirmation or error signal
By displaying the information digitally, the picker has both hands free and does not need to constantly look at the printed list of goods which improves workplace ergonomics and prevent delays in the picking process.
AR-supported picking methods become particularly efficient when used in conjunction with barcode and RFID scanners, such as those on the smart glasses themselves or in a ring, wristband, hand scanner, or glove. In this instance, a barcode is scanned, or a signal is read via RFID when items are picked before the removal of the goods is automatically booked in the merchandise management system. Once the goods have been compiled, packed, addressed to the customer, the order is automatically recorded in the system as ‘completed’. Subsequently, an automated notification of the upcoming delivery, including the invoice, can be sent to the customer without detours.
Seamless supply chains end-to-end
Unlike manual processes with printed lists, Vision Picking technologies enables a seamless, uninterrupted, and therefore an error-free flow of information from order to transport. Because information never has to leave the digital environment, minor disruptions occurring from manual processes (such as printed lists) are omitted. The use of barcodes and RFID ensures that all desired parts of a delivery are accurately picked, so customers receive the complete order, and goods do not accidentally get misplaced.
Furthermore, by confirming the removal of items, the stock and the status in the merchandise management system always remain up to date. This results in more efficient warehouse management as stock is not wasted, and warehouse managers can ensure the re-ordering of goods is as demand oriented as possible. Operating at minimum stock level is an important indicator of efficient warehouse operations. Through using intelligent and automated storage systems, warehouse managers can fill racks very easily. If an item falls below the defined minimum stock level, a recorder can be automatically triggered. Through implementing these technologies, supply chains can undergo a successful digital transformation and put gain competitive advantage.
Increased efficiency for employee and employer
Digitizing processes such as picking isn’t just crucial for the business and bottom line but also benefits employees. In the example of Vision Picking, staff are no longer required to conduct an extensive search around warehouse for the right shelf or compartment. They are shown where to pick an item via directional instructions to find goods as fast as possible, all without special training. These benefits do not just apply to picking by hand. Vision Picking also enables forklift drivers, for example, to get directional instructions projected directly into their field of vision and don’t have to take their eyes off the road to check a paper list. This improves the ease, safety, and efficiency of their job. Implementing digital solutions into the supply chain, therefore, has holistic benefits for business. It does not just help create a healthier, more resilient supply chain, but also enhances employee performance, which in turn leads to more engaged and satisfied staff. This is critical as businesses rely on their employees to meet the high demands of a post-pandemic era.
Futureproofing the supply chain
In the age of pandemic recover, the supply chain can no longer afford to not be digitally led. Through technologies such as Vision Picking, companies can bridge the gap between humans and IT systems, optimize processes, increase efficiency, and relieve the burden on employees. Supply demands are not slowing down soon. It’s time for supply chain managers to future proof their businesses to steer growth, mitigate errors, and create a seamless experience for all.
Hendrik Witt is CPO at TeamViewer, a leading global technology company that provides a connectivity platform to remotely access, control, manage, monitor, and repair devices of any kind – from laptops and mobile phones to industrial machines and robots. Although TeamViewer is free of charge for private use, it has more than 600,000 subscribers and enables companies of all sizes and from all industries to digitize their business-critical processes through seamless connectivity. Against the backdrop of global megatrends like device proliferation, automation and new work, TeamViewer proactively shapes digital transformation and continuously innovates in the fields of Augmented Reality, Internet of Things and Artificial Intelligence.
www.teamviewer.com