Why collaboration is the secret to achieving Net Zero
Global businesses are under pressure from several stakeholders – customers, partners and governments – to cut carbon emissions and contribute to the world’s critical mission of reaching Net Zero. This is confirmed by 66 percent of UK organizations recently surveyed by Wincanton. Doing so doesn’t happen overnight, but some companies are worried they won’t make it at all, with over half (54 percent) revealing they will struggle to meet net-zero goals.
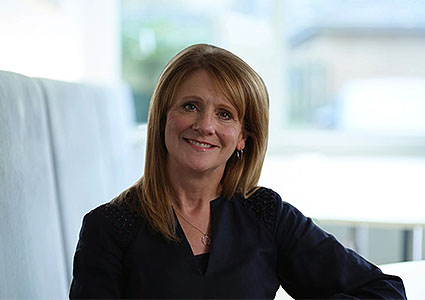
But we can’t afford to wait – time is already ticking as temperatures rise across the world. According to our survey, 83 percent of respondents say logistics is key to achieving their net-zero goals. However, costs and concerns about the viability and availability of alternative fuel vehicles are holding them back. The good news is there are ways businesses can reduce emissions in their supply chain operations while new fuels are being developed – and without breaking the bank.
Sustainable progress doesn’t mean high costs
Four in five (80 percent) respondents in our survey believe that reducing carbon emissions in their logistics fleet means an increase in costs. As a result, two thirds (66 percent) have had to deprioritize hitting their net-zero targets. But our research suggests reducing emissions doesn’t necessarily translate to a rise in costs, as 37 percent say they have seen cost reductions from tackling emissions. Clearly, there’s a perception gap when it comes to the costs associated with reducing carbon emissions.
There are opportunities for businesses to both cut costs and reduce emissions simultaneously. In the EU, one in five HGVs on the road are empty and a similar problem is seen across the Atlantic, as 15 percent of the total kilometers travelled by HGVs in the US are empty. Too much fresh air is being transported around the world, incurring high costs for businesses and limiting their ability to hit sustainability targets.
Businesses should leverage technology that reviews their loads and route planning. That way, they can make productivity gains and reduce empty running. Doing so means businesses can increase cost efficiency while contributing to a greener world.
Alternative fuel vehicles won’t save us… yet
Alternative fuel vehicles aren’t quite ready for widespread adoption. Of an international fleet of 12.2 million HGVs, only 13,000 are electric – representing just 0.1 percent of total HGVs on the road. There’s a long road ahead, which is why only a quarter (25 percent) of logistics and supply chain directors think alternative fuel vehicles will be affordable in four-to-six years.
Extensive research and investment are going into electric HGVs and vehicles powered by biofuels and hydrogen, but businesses can’t wait that long to improve the efficiency of their vehicles.
The answer lies in collaboration
Better collaboration can improve sustainable performance across the board. Two-thirds (65 percent) of survey respondents agree collaboration is key to the future success of the logistics industry and will help to tackle a range of issues, including reducing costs and cutting emissions. This could explain why 61 percent are already collaborating and a further 32 percent are planning collaboration opportunities.
However, collaboration needs to be made easier for all involved, as businesses say they’re nervous about experiencing difficulty in either finding partners to collaborate with (28 percent), or the lack of internal resources to manage collaboration projects (26 percent). Collaboration translates to access to a community of transport providers that can increase operational efficiency and improve resilience. Technology provides insight and benchmarking on what others are doing, equipping businesses with a wider view of the whole industry to know how and where they can be doing things better.
Collaboration and technology investments may sound daunting, but this is where a logistics service provider (LSP) can add value. LSPs can provide the knowledge, technology, and expertise that businesses can’t match, allowing them to focus on delighting customers with timely, sustainable, and cost-effective deliveries.
For a list of sources used in this article, please contact the editor.
Helen Flanagan is the Product Director of EyeQ at Wincanton, Wincanton’s digital transport solution. With a deep knowledge and passion for digital solutions and data analytics, Helen is constantly developing internal products and helping businesses implement innovative technologies to solve problems and reach net-zero goals.